





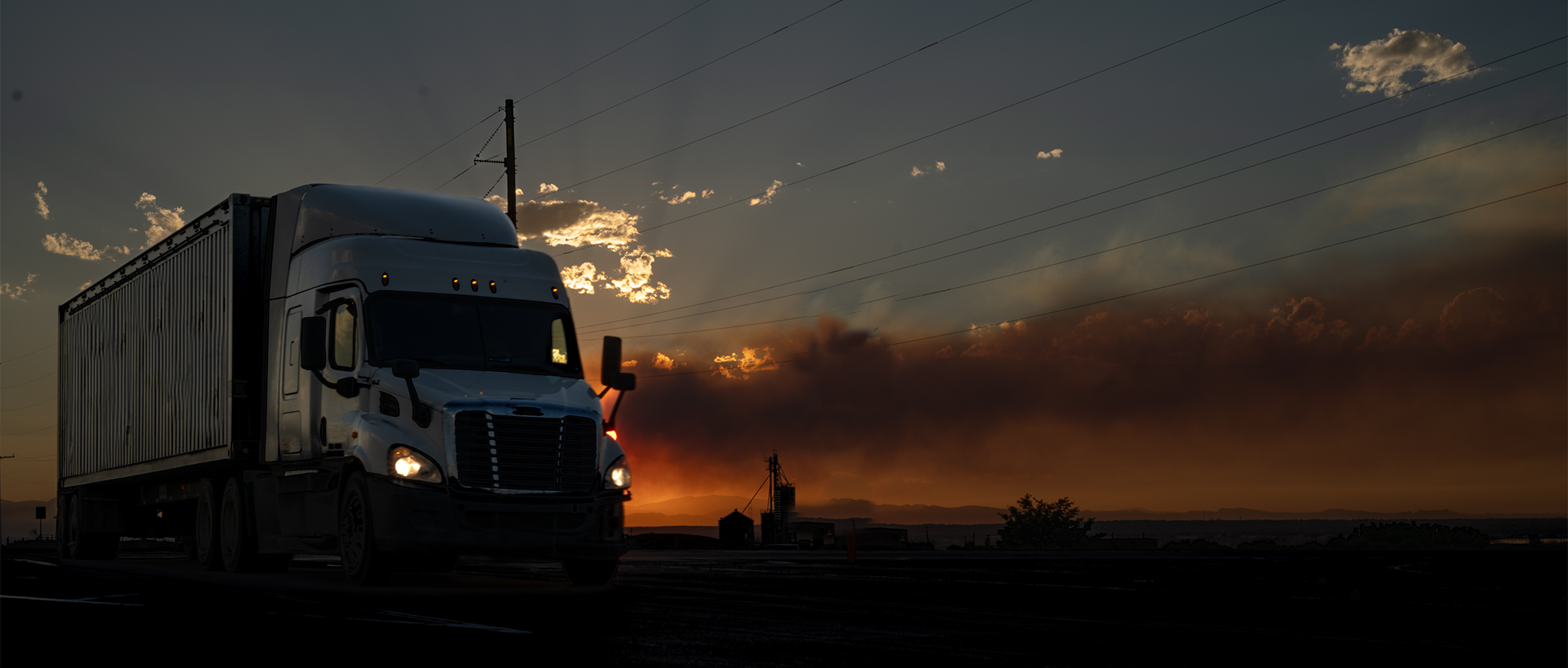

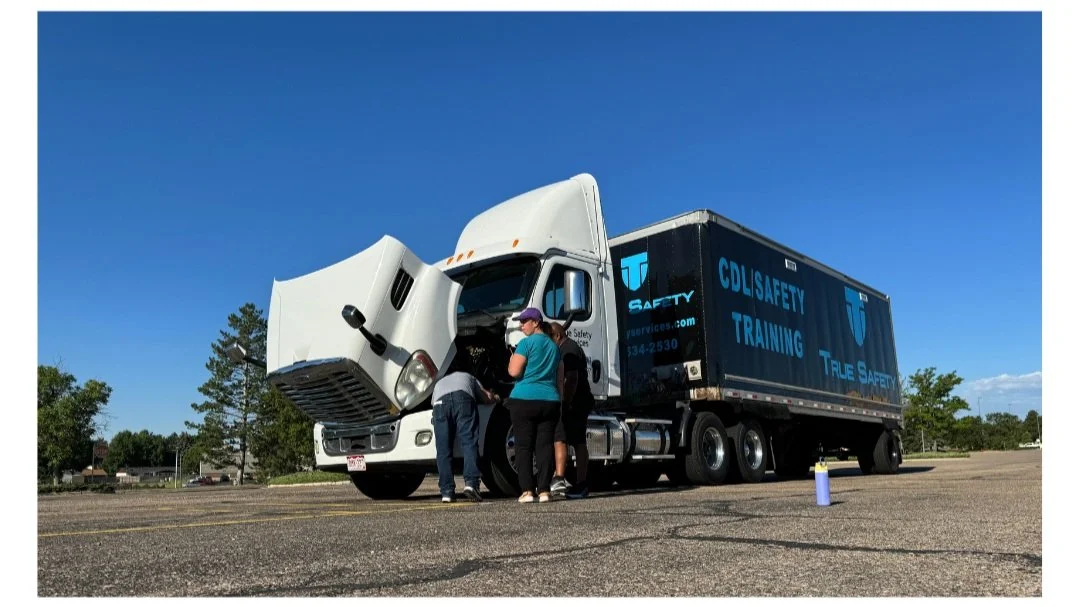
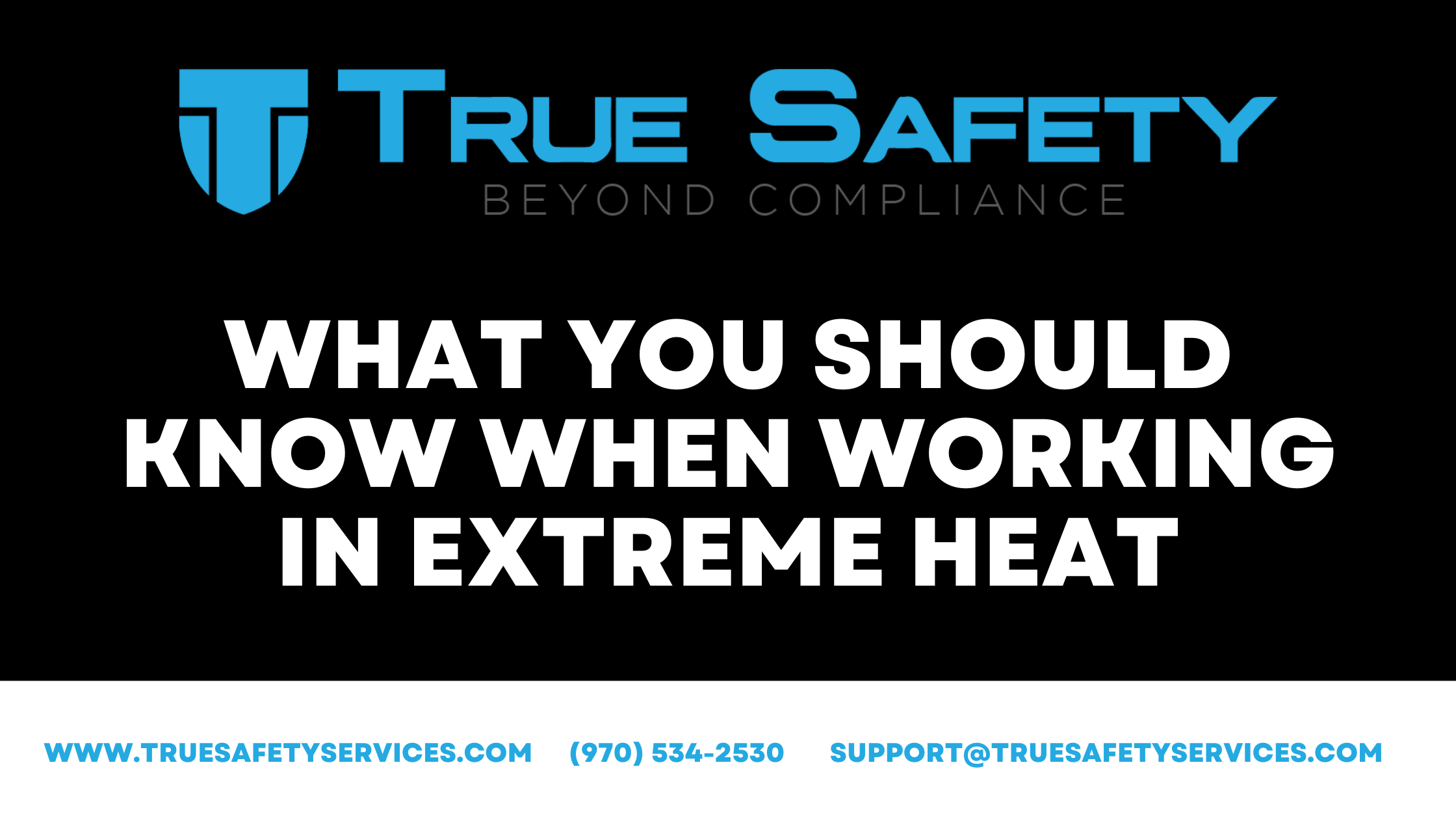
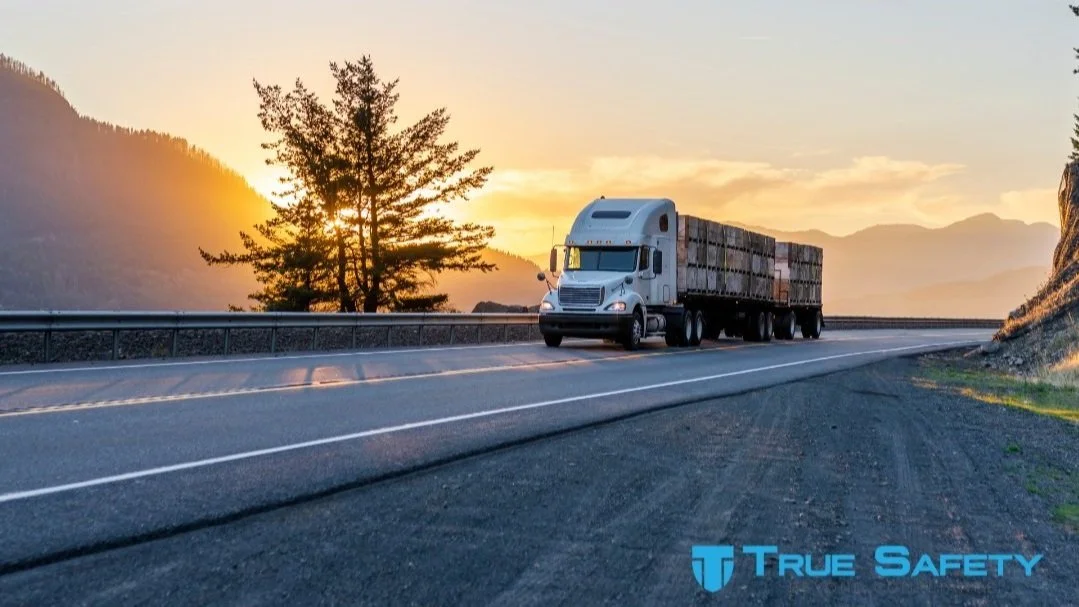
Why the Open Road is Calling: A Fresh Look at the CDL Industry
A deeper dive into the benefits of a career in the trucking industry.

Mental Health: Across the Blue-Collar Industries
Mental health has long been a critical, yet often overlooked, component of overall well-being, especially in blue-collar industries.
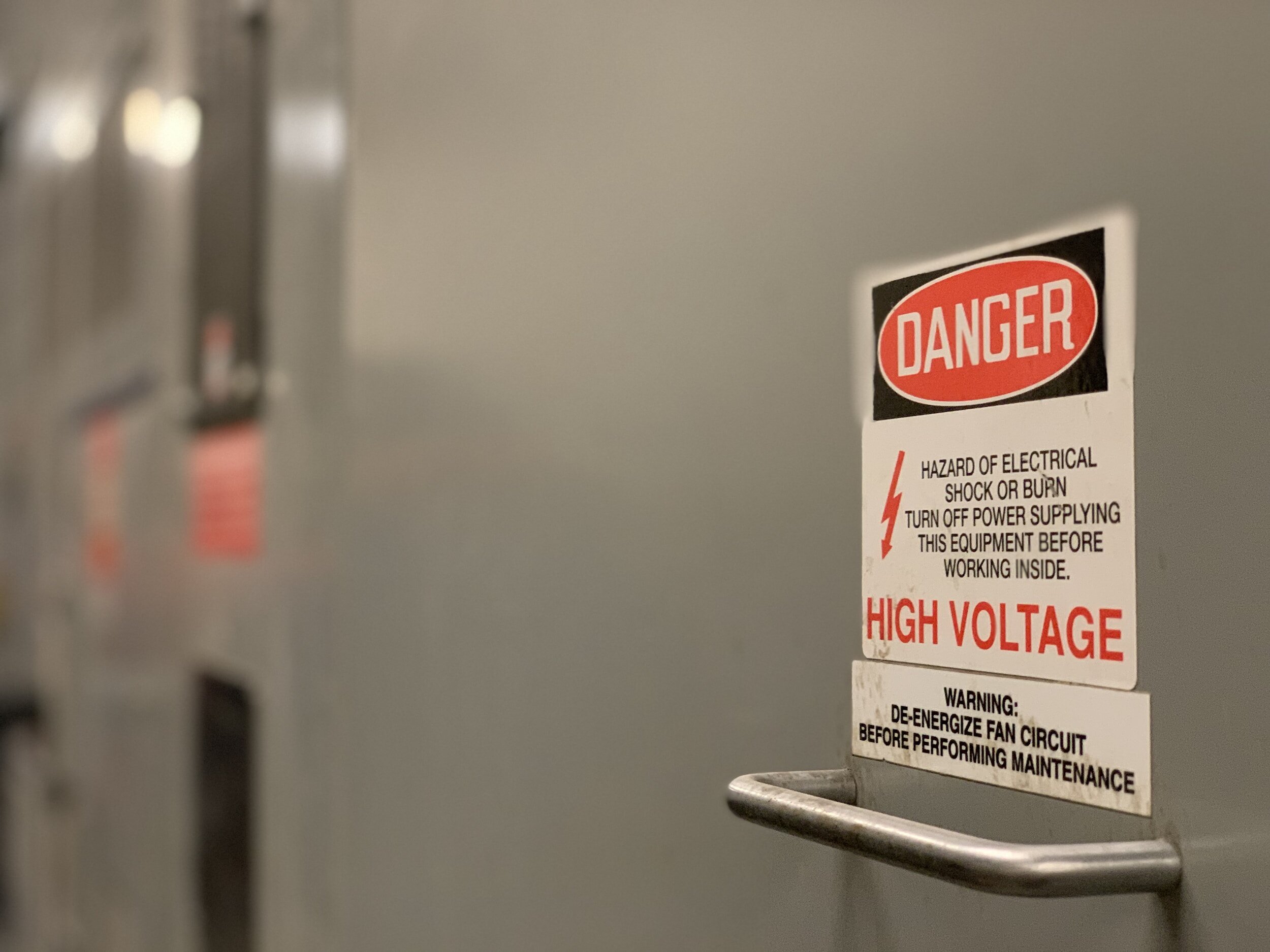
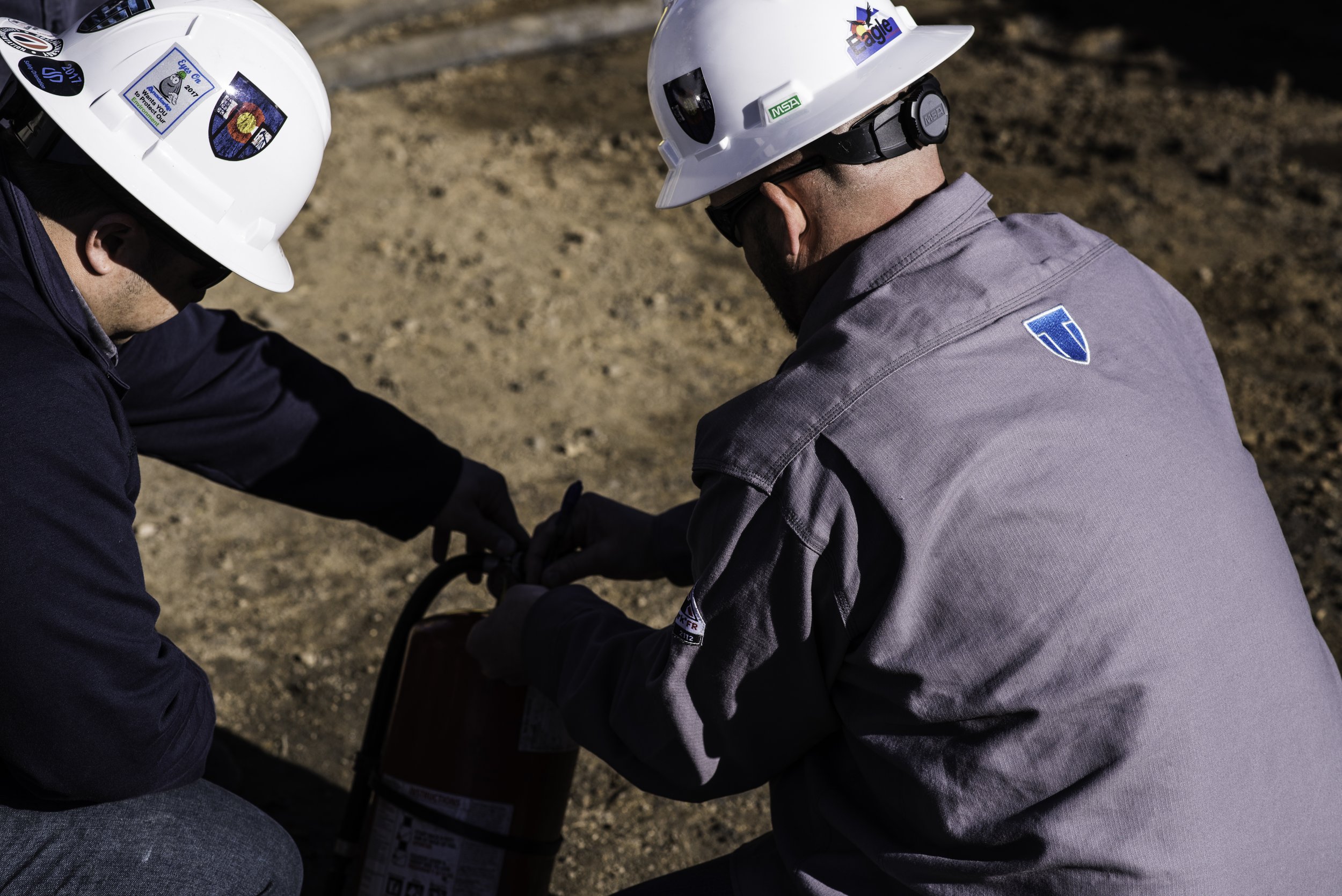
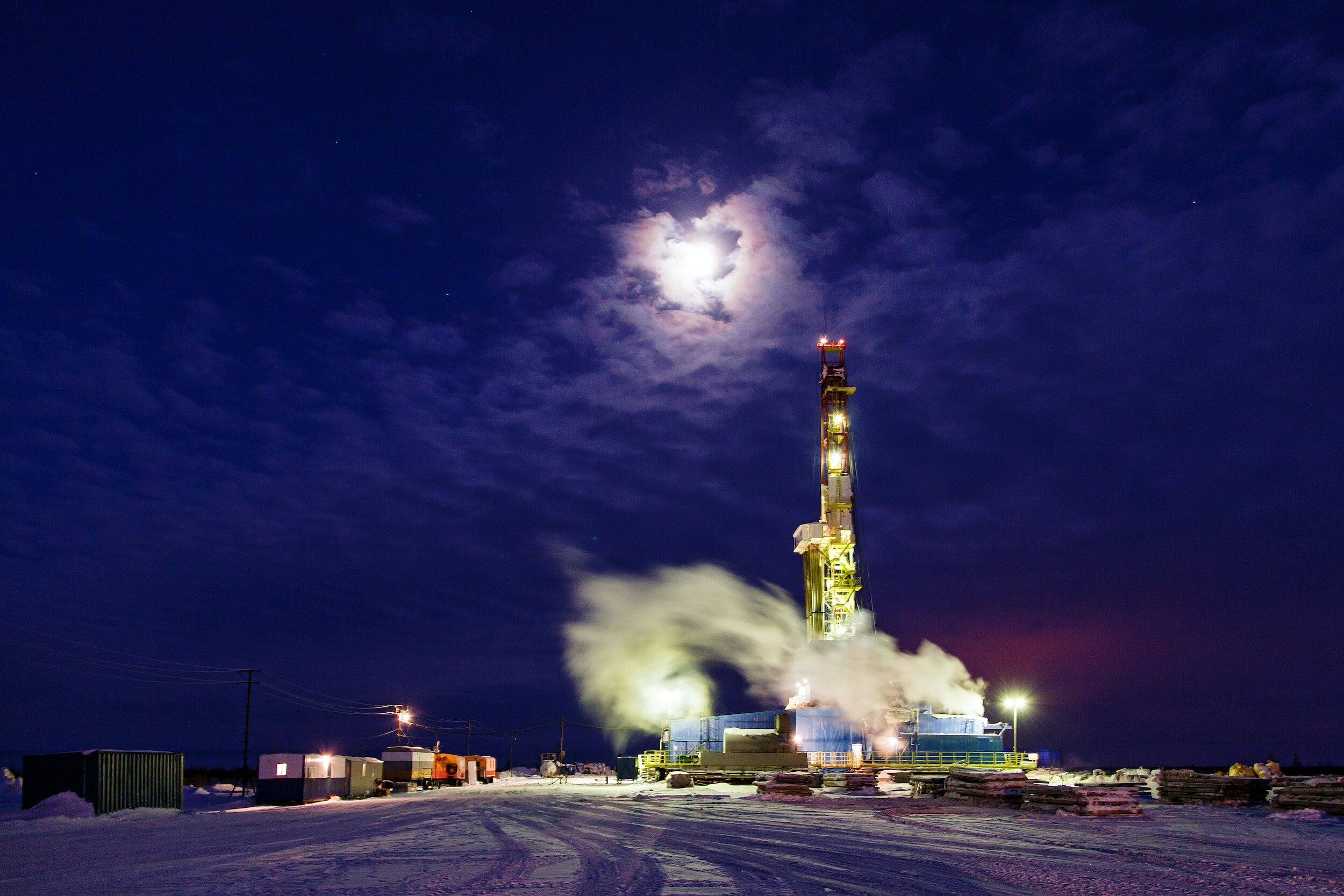
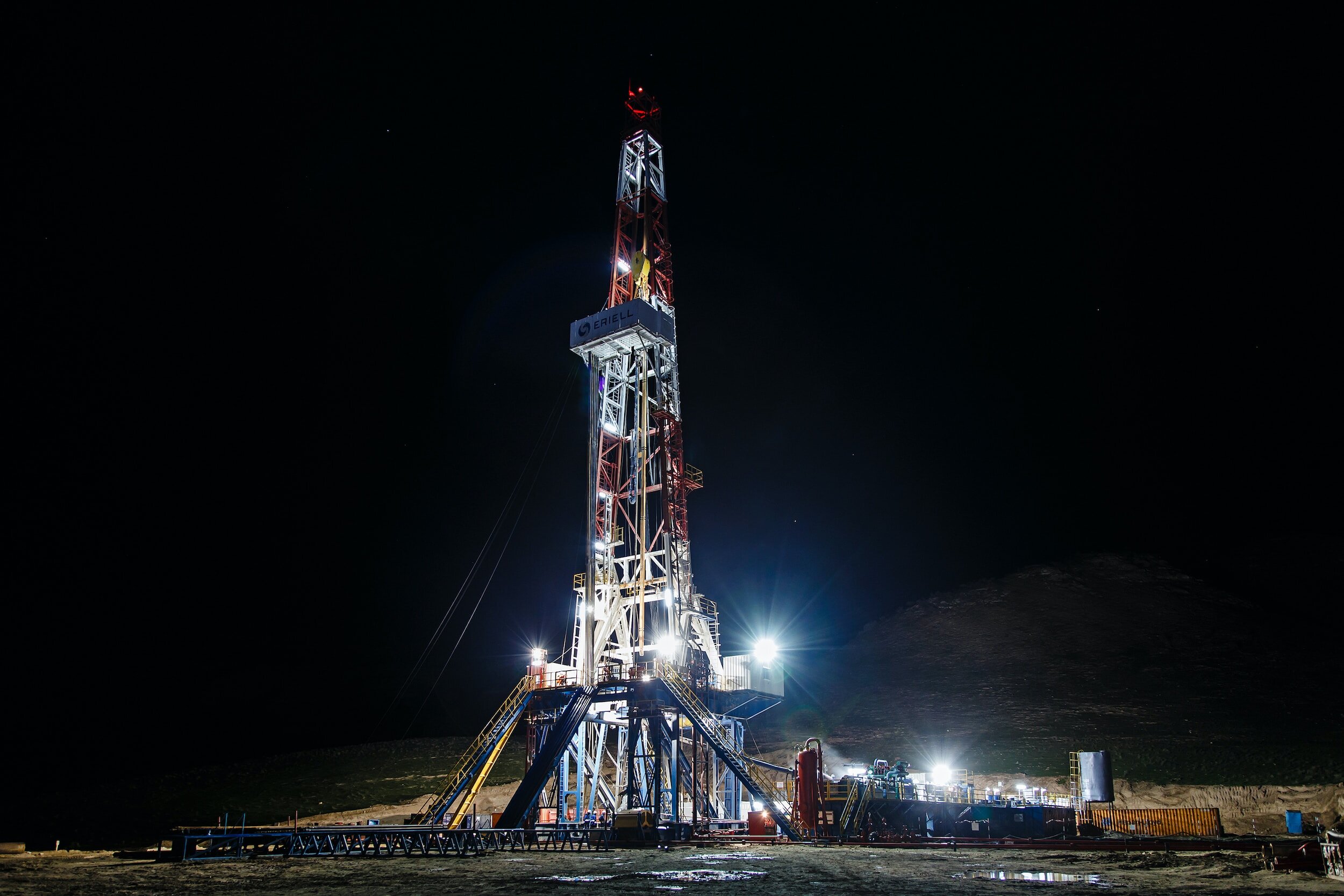
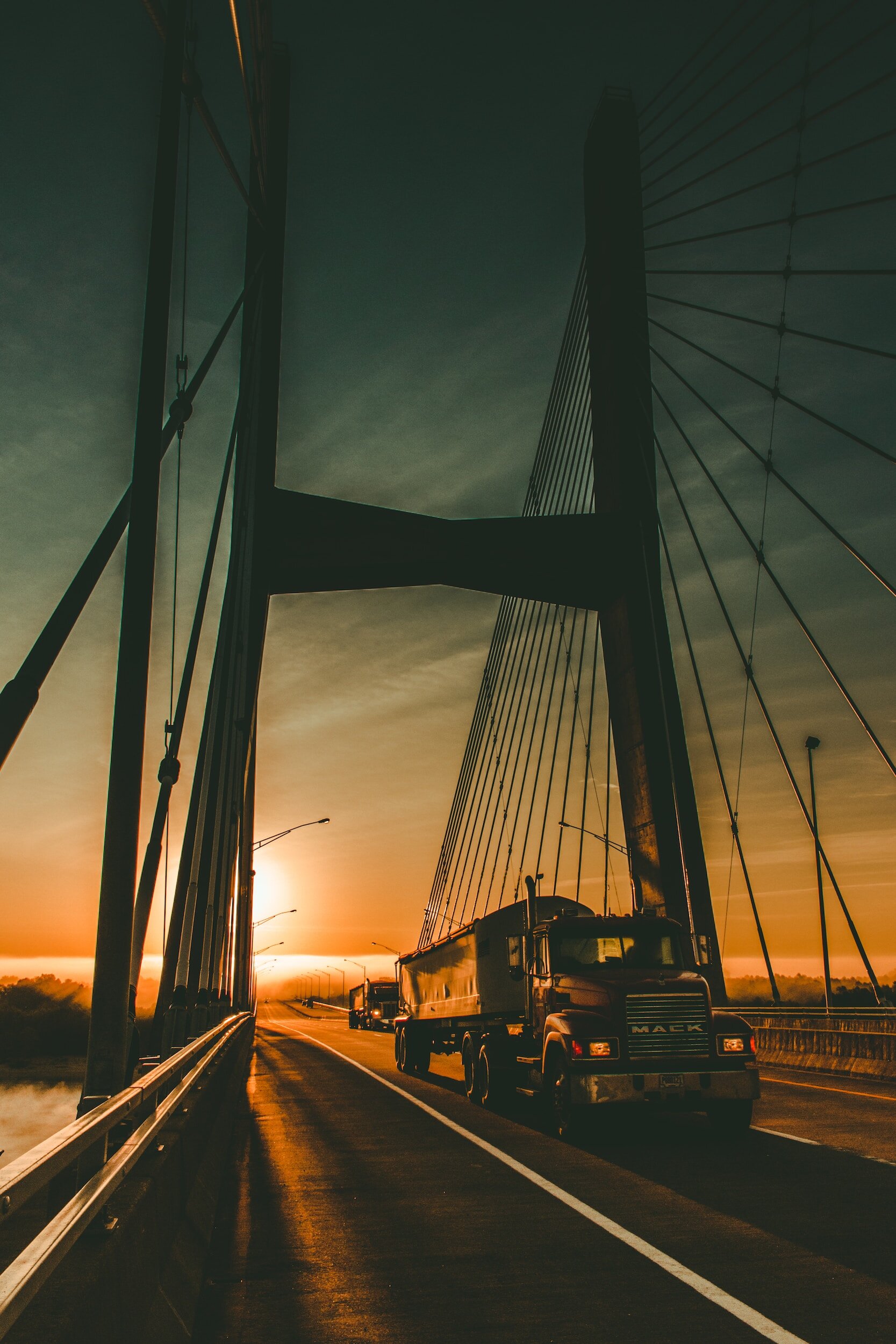
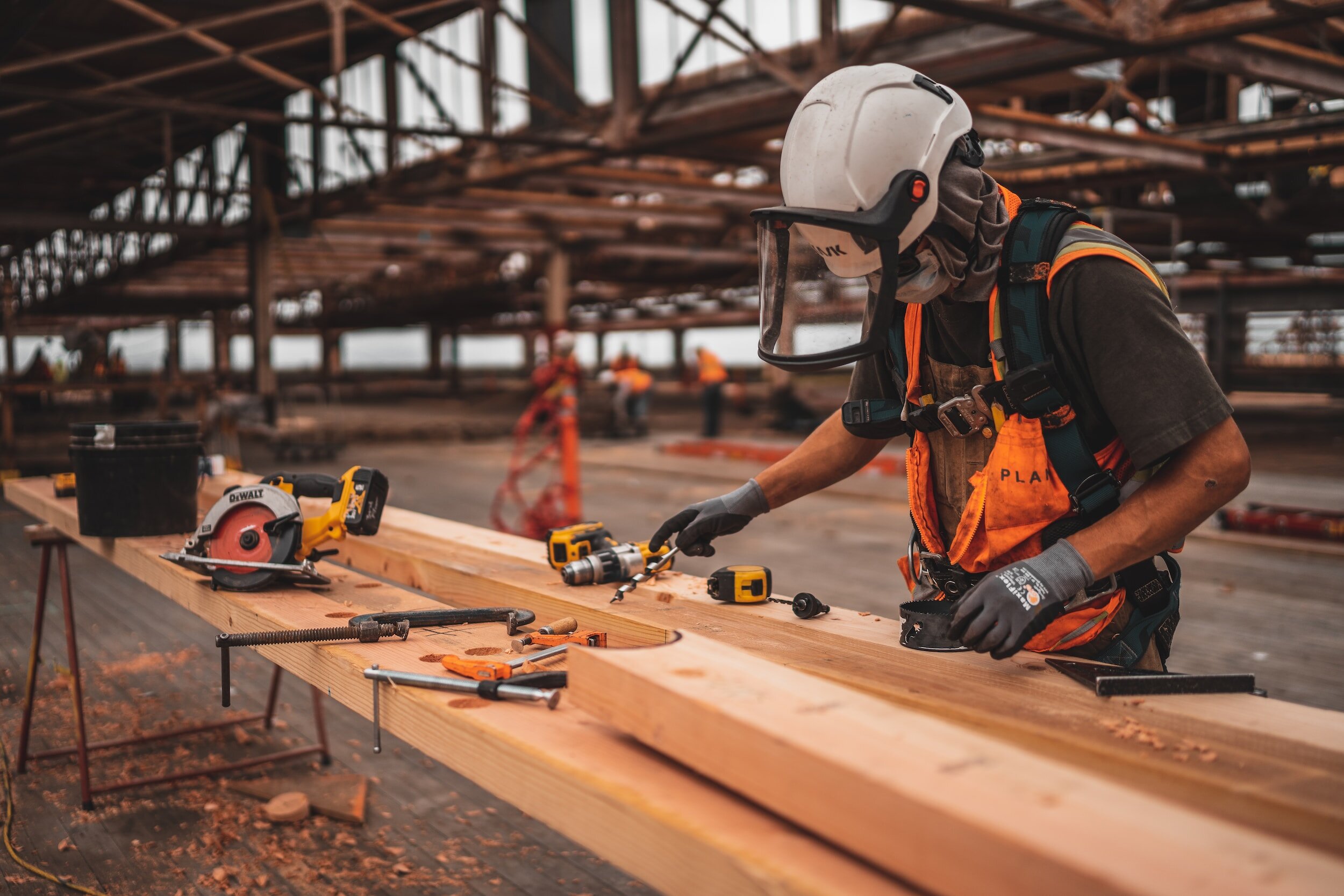
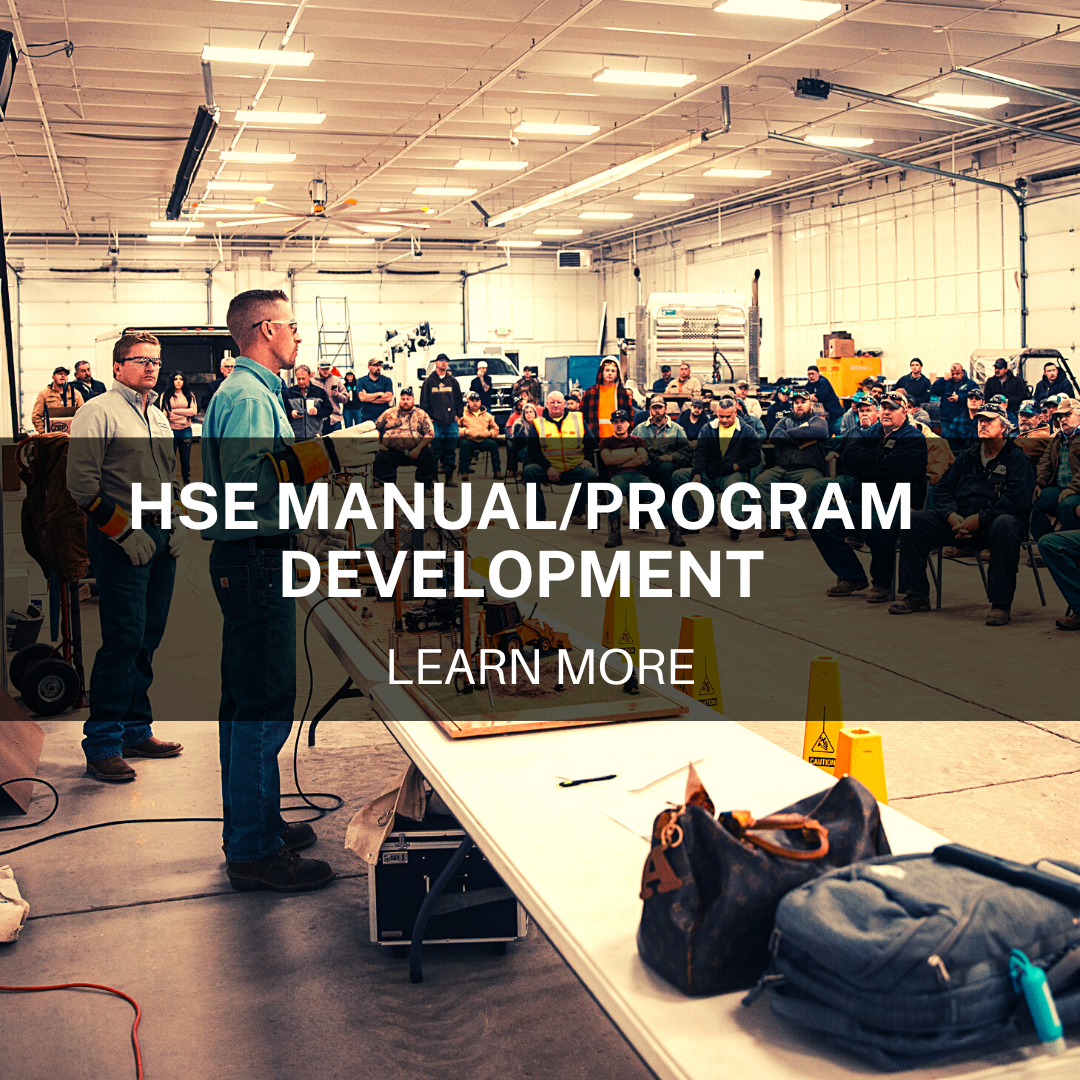
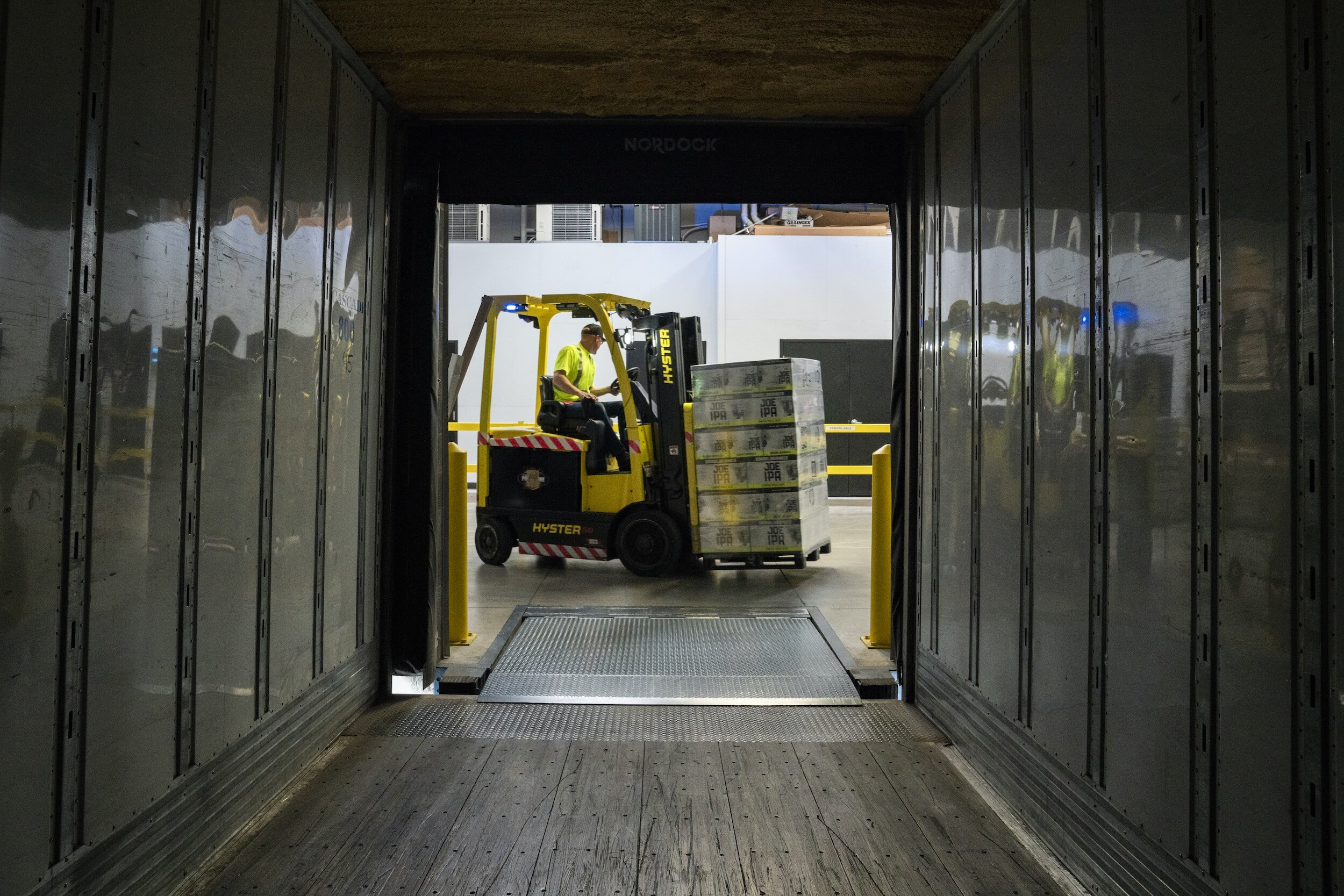